Introduction
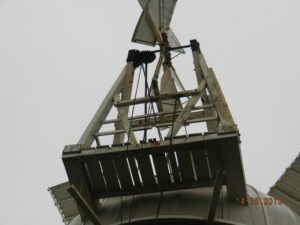
Our millwright – Traditional Millwrights from Lincolnshire – came on 12th August 2015 for a routine maintenance visit to paint and check mechanisms etc. While working on the wooden fan staging spar (which supports the fan) they found some severe wet rot, partially hidden by the paint covering.
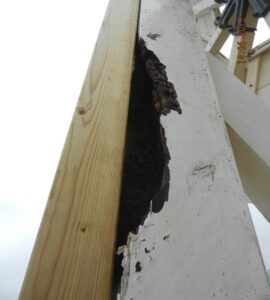
As a result of this they looked at the exposed timbers at the front end and found severe rot in the weather beam (rode baulk), the centre mullion and parts of the exposed main sheers.
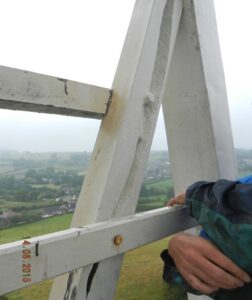
These parts had not been replaced during the 2000 restoration but had been adjudged to be suitable for continued operation.
(Note for info only – the two main sheers were replaced by Derbyshire County Council in October 1997 and a lightning conductor was fitted at same time).
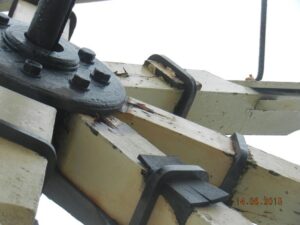
The paint on the centre mullion indicated this may go back to the 1894 restoration. (A series of photos at the end of this report show the damage as viewed in August 2015).
For reference purposes a drawing of the cap area is shown in Fig 1.
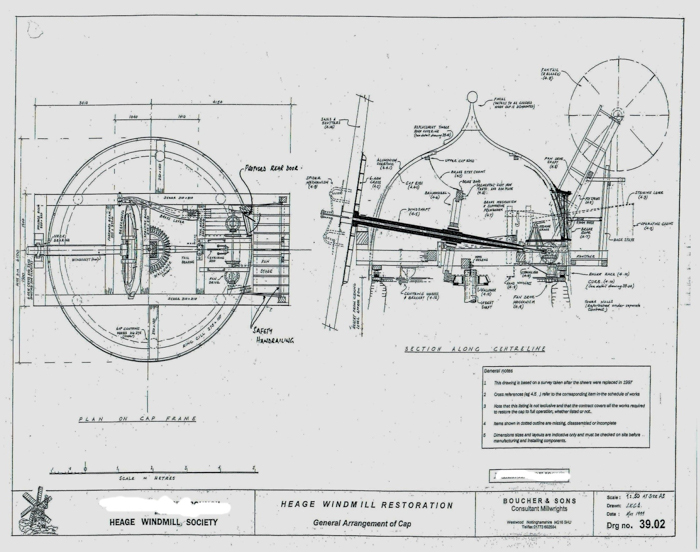
The cumulative effect was that the millwright fitted temporary bracing on the fan spars (supports) but also recommended that we did not continue to operate the mill until repairs had been carried out. Their preliminary estimate put the cost, including repair and painting of the sails, at around £90,000- £100,000.
This note is intended to record what actually happened, or what materials were used, for future reference.
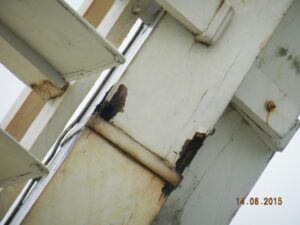
Action Taken
An emergency meeting was called at the Mill on August 17th attended by all available Trustees and Friends, with over 30 being present. Three options were considered:-
- Do nothing, close the Mill and hand back to owners, Derbyshire County Council ((DCC).
- Keep the mill open for visitors but not turning the sails and no flour making until sufficient funds are raised.
- Raise funds for repair as quickly as possible and get on with it as quickly as possible.
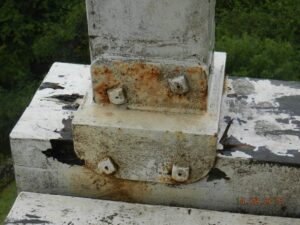
There was huge support for option (iii) and the Heage Windmill Society (HWS) Trustees decided – with full support of the Friends of the Mill – that based on advice from the millwrights, they would continue to open the mill to the public but would not be turning the sails, or mill wheat, until repairs had been completed, if at all possible during the winter closed season.
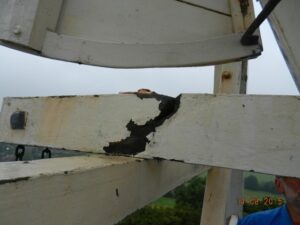
The work was initially estimated as costing in excess of £90,000, a sum far above the reserves held by the Trust. Grants and support would therefore need to be sought to enable the work to go ahead and various fund raising activities needed to be organised.
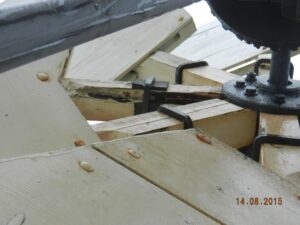
To manage the repairs two teams were formed.
Operations – this dealt with the actual repairs.
Fund Raising – to raise funds! The target given to both teams was to get the mill operational for the start of the 2016 season, if at all possible.
Preliminary ‘Operations’ Activities
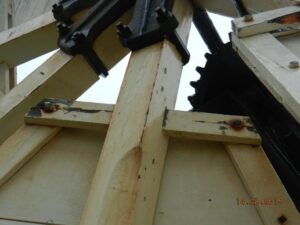
A meeting of this group quickly decided that in view of the cost of the work a further professional opinion should be sought and the now late Vincent Pargetter, an eminent nationally recognised millwright, was employed to carry out a survey and express his opinion (Cost £450). He generally agreed with Traditional Millwrights’ concerns but also found an area of the cap circle (the frame that supports the cap structure) needed replacing. He made a number of other suggestions which were investigated and adopted where possible.
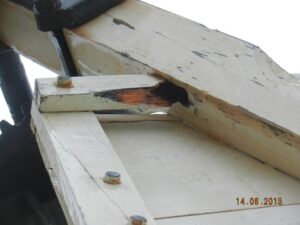
The use of Greenheart timber for the main supports (as suggested by Pargetter) was considered but eventually rejected due to listing concerns (and potential delays) from Historic England, as was the use of copper sheeting to protect the exposed sheers, instead of lead which had been used in the past. The group also considered the use of a fabricated weather beam (which would have been quite feasible) but again deferred due to Historic England listing concerns. It was, however, agreed to use stainless or galvanised fittings wherever possible. Based on the two millwrights’ reports a specification for the work required to be carried out professionally was prepared by John Boucher (Appendix 1) and submitted to five millwrighting firms. Three were too busy and another pulled out later.
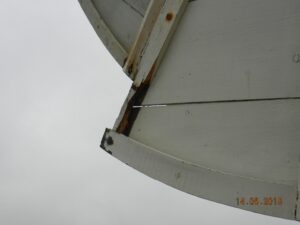
The group considered extending the work over a longer period (i.e. multiple phases) and also assessed the total work content involved. They decided that the sails could be repaired and painted by mill volunteers since this represented a significant part of the MW estimate. It was therefore agreed that an external, nearby workshop area should be found where the sails could be worked on. In due course arrangements were made with the owner of Ambergate wire works that we could have the use of one of its empty bays, at no cost to the Mill.
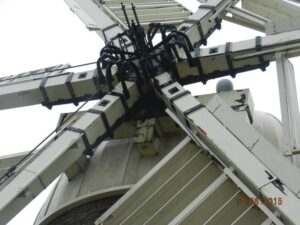
In the meanwhile only one firm bid for the work: our current millwrights, Traditional Millwrights. After some negotiations involving selection of materials and work to be done by our own volunteers, an order for work was placed, with a target to be completed by Easter 2016.
Funding Activities
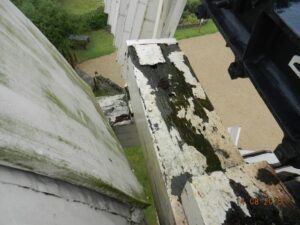
The Funding Group were targeted to raise at least £50,000 and immediately launched a donations scheme called TAMA (Trouble at the Mill Appeal) and organised ‘bucket’ collections at local pubs etc. and at the mill, which itself remained open until the end of October to help earn some income. Establishing a web donation mechanism proved rather tedious and took some time to get established but in due course this, together with Social Media produced a steady flow of income.
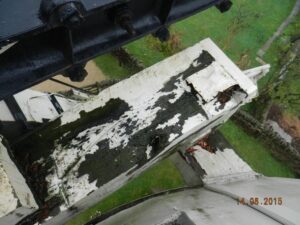
To many people the obvious place to seek funds appeared to be the large grant making organisations, such as The Heritage Lottery fund etc. but we soon hit a brick wall!
These organisations
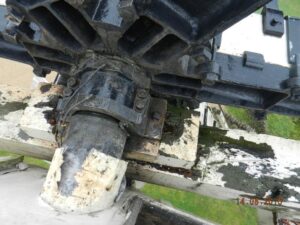
have a strict protocol to be followed in making grants and generally had long lead-in times; coupled with the fact that applicants cannot start work on a project until a decision to award a grant is made.
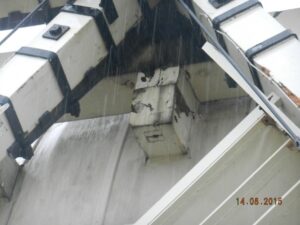
They did not have a ‘fast track route’ to deal with an emergency such as Heage Windmill faced.
The awarding of grants was also problematic because at the time of our enquires we did not hold a long term lease on the Mill with the owner, DCC and could not demonstrate security of tenure. (This has since been determined in February 2016).
A Trust decision was therefore made to proceed with the repairs, as a single stage operation, without seeking any major grants, in the hope and expectation that the necessary fund raising target could, and would, be achieved.
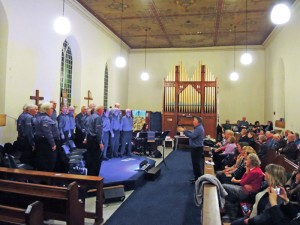
All current supporters, and many past visitors to the mill, were invited to make contributions to help match the shortfall in funds, seeking to raise at least £60,000.
All types of fund raising events were held over the coming months, ranging from choir concerts to book sales, to coffee mornings and the sale of wrist bands.
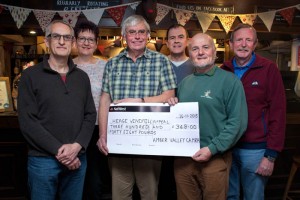
There was even a bucket collection at a beer festival and a raffle for a donated local holiday property!
Two choirs gave free concerts in the local church, which raised funds.
The proceeds from a very successful Santa Day were also added to the fund.
A steady stream of money was forthcoming, with much goodwill in the neighbourhood of the mill resulting from a house-to-house leaflet drop. Donations were received from all over the country from mill bodies, mills and even internationally. The total raised was finally boosted by two large donations of £10,000 each from the owners of the mill – Derbyshire County Council – and from local business Bowmer and Kirkland. In all £57,337 was raised in less than nine months. (Sept 2016)
Operations Group Activities
a/ Sails
The Trust had previously intended to paint the sails during 2016 and the opportunity of removal was used to get this work done, following the discovery of rot.
Local contractors Nicholls Hydro Engineering Ltd., were employed to remove the spider gear etc. and the sails. This was accomplished over several days and the actual sail removal – by a crane employed by the contractor – was assisted by a team of about 10 volunteers.
The leader boards were removed from each sail to facilitate handling and they were stacked on their backs in the car park, as a block, pending removal to the local work shop. This cost a total of £1914.
Arrangements were then made with local contractor J C Balls for the use, free of charge, of a driver and a Hiab (crane) equipped lorry. The six sails just fitted in the width of the lorry and were lifted and loaded, together with the leader boards, by volunteers and taken to Ambergate old Wire Works.
It had previously been recognised that the doorway into the Ambergate workshop was too low to allow the loaded lorry to enter and a small wheeled trolley had been made on which the sails could be loaded and then man-handled into the work area. After a few abortive efforts a system was developed and the sails were unloaded in about six hours by the volunteer team, numbering about 12, and pushed into the work place.
The sails, which weigh approximately one ton each, are identified as A through F and shutters are numbered 1- 126.
The known details of the current sails are as follows:-
Sail Code | Material | Installed |
A | Laminated (Siberian Larch) | 31- 3-2006 Marked N2006M |
B | Not Known – Solid wood- pine? | Not Known but probably 1996/7 |
C | Laminated (Siberian Larch) | Made NM 2007 |
D | Laminated (Siberian Larch) | 31-3-06 Marked N2006M |
E | Not Known –Solid wood- pine? | Not known but probably 1996/7 |
F | Laminated (Siberian Larch) | ? Marked N2006M |
Each sail was examined and details recorded on a separate pre-printed log sheet and an assessment made of any repairs needed. This assessment was confirmed by our millwright before work started.
Essentially the four laminated sails (A,C,D,F) were generally found to be sound although some open shakes needed to be cleaned out and heavily primed before painting.
A large insertion of Douglas Fir (taken from sound old whip) was needed near the heel of sail B to replace some rather deeper rot and a piece of this wood, some 4 inches square x 48 inches long, was sealed in place.
It was closely bedded into the cut-out from the whip and sealed in placed with a two part epoxy resin, tightly clamped until set, thus forming, in effect, a section of laminated timber.
A much smaller triangular insert was also made on a corner of sail E. These should be monitored on a biannual basis.
In several other places superficial corner rot was found on whips and ground out smoothly before painting. On sail E superficial rot on corners was ground out smoothly before painting.
Some repairs, replacements and scarfing in of new timber were needed on parts of the framework of both the older sails but this was essentially considered sound on the others. Again, monitoring of all the sail frame work must be considered an ongoing action.
The 126 numbered shutters were all made in 2001/2 and consist of a wooden back bar, with a stainless frame inserted, over which heavy duty painted canvas was hand sown. These are generally in good condition although there was quite a lot of green algae in the bottom edges, where moisture had lodged. This was removed by spraying with domestic Flash cleaner and then brushing to clean before painting. In view of this potential source of future trouble, consideration should be given to an annual inspection of shutters, in situ if at all possible.
The work, including painting the sails, leader boards and renumbering the shutters, was done in the period November to March and involved over 600 man hours. The paint used was as specified by the Millwright (Kreidezeit Stand Oil) and an initial estimate was made for the sails only ( Appendix 2) .Our ‘master painter’ on completion of the work commented:-
‘The average paint coverage is about right .The two older sails had more paint applied to them, because of the shakes and repairs pointed out by John B. Primers and undercoats and as many coats of finish required were used to fill in the shakes, therefore we used a higher figure than originally estimated. I always apply more paint per square metre than usual (as quoted on datasheets) in order to achieve a higher quality and better finish.’
A check at the end of the work showed we had 1 litre of primer, 3 litres of undercoat and 1.5 litres of top coat as surplus.
All the nuts bolts and fixings used in the sail restoration were donated by a local company, TT Fixings from Meadow Lane Industrial Estate, Alfreton.
When the work was completed J C Balls again provided the Hiab lorry and driver, and work was facilitated since another contractor on site provided us, free of charge, with a forklift truck and driver. This was very manoeuvrable in the limited space available and greatly speeded up the loading operation. The sails were taken back to the mill site and again stacked and made secure, ready for fitting by the millwright.
(Millwright estimate for sails work, including removal and transfer to his workshop was £27,100 plus Vat)
b/ The Cap
It had been the Trust’s intention that the cap be painted during 2016, to be carried out by the millwrights. However the volunteer team decided that since they had a master painter and two persons trained as ‘cherry picker’ drivers in their midst, they would carry out the work themselves if at all possible. They established that a local business had such a device which could be made available, free of charge to the mill, at weekends only. Since the sails were not yet in place this meant that there was almost complete free access to the full circumference of the cap.
The weather was favourable in April and, over two weekends, the work was completed from the picker with one coat of Kreidezeit Stand Oil under coat and one of top coat paint, using either a small roller or a long handled angled paint brush, as appropriate. The cap was soon noted on the web as ‘gleaming in spring sunlight’. The millwrights also carried out work to seal some leaks at some joints in the circular gutter.
Note – Millwright estimate for one coat of paint (Kreidezeit Stand Oil) on the cap was £1945 plus Vat
c/ The Paint
The sails and other wood work had been previously painted with a water-based Acrylic paint, believed to be Excel 40 shade. This had clearly not been entirely successful. The paint chosen for all current work was Kreidezeit Stand Oil paint made from linseed oil, stand oil, Portuguese balsam turpentine oil, zinc oxide and other mineral pigments. Details of the paint used is included as Appendices 3 & 4.
Overall, rather more paint was needed than the initial estimate and further orders were placed such that we would have enough to paint the cap.
Note 1 – it was recommended that painting is done at 8 degrees C minimum. Fortunately we had a mild winter period and were generally able to comply with this. Even at lower temperatures, but when still above freezing, the paint was applied and dried quite well inside the workshop.
Note 2- The total cost of paint, and other materials used by volunteers was £2,228 – split between sails and cap – possibly 25% of the paint ordered was used for cap but no direct record was kept.
Work by Millwrights
The division of work between the work to be done by the millwrights (MW) and the volunteers was clearly defined, although both groups helped each other, as best suited the situation.
The MWs first removed the disconnected fan drive from the cap internals and then removed the fan. They next de-mounted the entire fan support structure, which was to be replaced in its entity, and lowered it to the ground. In fact two arms of the fan itself broke off due to rot whilst being removed- a near thing perhaps! It was then loaded onto a lorry and taken, with the fan, to the MW’s workshop and these were used as patterns for the new ones, made in oak. The condition of the exposed sheers was then assessed and they were found to be in reasonable condition, requiring very little work to keep them going.
At the front end, with the sails already gone, access to the weather beam etc was open. The wind shaft was jacked up internally and supported on a profiled piece of timber, to enable the beam and the centre support mullion to be removed and lowered to the ground. The condition of the sheers was not quite as bad as anticipated but a section of rot was carefully cut out and replaced with oak inserts, set in epoxy resin. As a precaution this should be monitored on at least an annual basis. Unfortunately when the front 10 inch diameter Bronze bearing itself was examined it was found to be broken in five pieces and needed to be replaced (with metal to BS1400 PB2, cost £560). This caused a delay of several weeks. There was some evidence that the bearing, at some time, had been turned 180 degrees in the cradle.
A new fan stage and fan were made at the MW works and large oak timbers were prepared and shaped to replace the defective front end ones. One large piece intended for the weather beam was rejected due to presence of large knot in a key area. The obtaining of the replacement caused a small delay in the programme.
These components were brought to site and placed in position using a large crane. The rotted section of cap circle was replaced but some problems were experienced in getting free rotation of the cap. The sails were replaced and set up without any major problems being encountered.
Summary of Proposed Actions
All Sails – generally monitor all the sails and frame work on annual basis, as a minimum, for breakup of paintwork
Sails A & E – inserts to be specifically monitored for condition on a bi-annual basis.
Shutters – Annual inspection of shutters to check for any build up of algae, or other damage
Sheers – inserts made on front and rear of sheers to be inspected on annual basis.
Fan and staging – Annual inspection of condition of paintwork
The date, and findings, of these inspections to be recorded in a ‘Mill Inspection Log Book’ – to be created.
Summary of Costs and Income
Millwrights fee was £62,373.60, including VAT (of which £561.60 was the replacement bearing at cost.)
Paint, materials etc was £4,706.70 (of which £1,914.00 was for Nicholls Hydro Engineering Ltd. who removed the sails)
Total cost of repair was £67,140 (excluding any credit and VAT for 100’s hours volunteer work if done by professionals and of the time spent by fund raisers.)
Fund Raising – In all £57,337 was raised in less than nine months.
Shortfall covered by HWS £ 9,900
Timescale of Events
The following listing of key dates is included to give an indication of the speed of the overall programme.
Date of last milling in 2015 18 July 2015
Millwrights visit 12 Aug 2015
Trustees/ Friends Emergency Meeting 17 Aug 2015
Date of Contract Award 24 Nov 2015
Sails removed 26 Nov 2015
Sails transported to Ambergate 3 Dec 2015
Sails transported from Ambergate 24 March 2016
Fan Tail Replaced 31 Mar 2016
Cap Painted Two weekends early April
Sails reinstalled 6 June 2016
Sails turned 22 June 2016
First milling session of 2016 27 Jun 2016.
Although the original target of Easter 2016 for completion had been established, a number of setbacks were encountered which resulted in delay to June 2016. These included
- Millwright being hospitalised for 2 weeks on the week the contract was set, followed by him being unable to drive for 6 months.
- A new large structural timber contained a large knot when delivered and had to be replaced.
- When exposed, the neck bearing was found to be in pieces and a new one, in phosphor bronze, had to be cast.
Despite these setbacks the project was completed to specification and under budget (by the use of volunteer labour).
Celebration Event
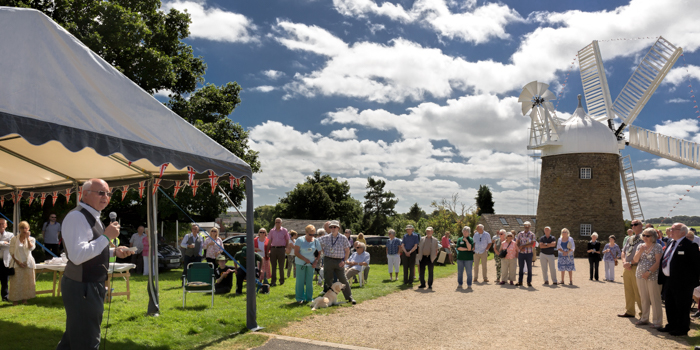
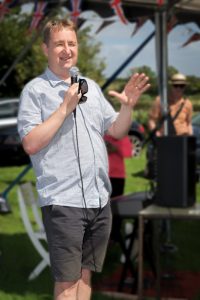
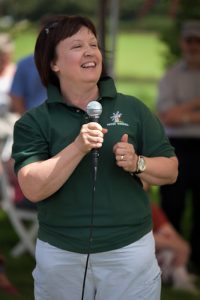
The Trustees decided on the successful completion of the repair that this had to be marked by a Celebration Event.
Such an event was organised on August 7th 2016, which turned out to be a beautiful warm and sunny day.
There was a gentle breeze and the sails, which were bedecked with garlands, turned slowly throughout the day.
All those present – some 120 attended – had contributed to the repairs by way of effort or financial backing, including of course our millwright Neil Medcalf.
The social event included a hog roast and two celebration cakes, one with a picture of the Mill.
The Trust Chairman Piers Bostock welcomed and thanked everyone for their support.
He was backed up by speakers from the Mill, DCC, the local MP and the largest individual donor, local firm Bowmer and Kirkland, who all praised the efforts of everyone involved.
Angela Ward, Chair of Friends of Heage Windmill, who had done so much work, responded, referring to the volunteers as a ‘Dream Team’ and said they had all (mostly) enjoyed the involvement but that above all it had brought everyone even closer together than before the happening.
And then everyone fed…………………………….
Comments and Recommendations
The entire recovery programme has been a tremendous exercise in team work from everyone associated with the mill, ably supported by local people and businesses. Support was also received from throughout the UK and even internationally. When faced with the problems back in August 2015 it would have been so easy to give up but ‘Team Heage’ prevailed and got the Mill back into full operation.
A spin off is that the millers have noted that the Mill appears to turn more smoothly since the repairs, possibly due to the bearing replacement. Work was finally completed on 22 June 2016 and milling took place again on 27 June 2016, less than 1 year after the initial wet rot discovery.
It is clear that we must be more proactive in looking after the Mill and a programme of regular, documented, programme of inspections and maintenance of key areas, such as the sails, shutters and exposed wooden structures, should be developed. The continued success of the new paint used in the programme needs to be verified before any potential serious deterioration occurs upstream.
Compiled by A F Gifford
(With input from Meg Tarlton, Alan Eccleston, Alan Clark, Danny Ashley and John Boucher.) September 2016
The ‘TAMA’ teams
The Fund-raising team consisted of:
Angela Ward, Ashley Franklin, Danny Ashley, Jack Evans, Lynn Allen, Nigel Vardy, Piers Bostock and Tony Cooper and Meg Tarlton
The Operations team was:
Alan Clark , Alan Eccleston, Alan Gifford, Brian Naylor, Danny Ashley, John Boucher, Piers Bostock and Stuart George with secretarial duties by Meg Tarlton
(With Piers Bostock on hand (most of the time) helping both teams .)
BUT these were just the nominated teams to get the project away. There were many, many more who helped get the windmill repaired .
Thanks are extended to each and everyone involved and the ‘Old Lady’ is really grateful to all who made the miracle happen!
Appendix 1
Heage Windmill- Specifications for cap repair works 2015
Timber
Timber for all applications shall be carefully selected of high quality suitable for its function. The weather beam, sheer planks, mullion, pillow and packing blocks exposed to the elements at the front of the mill shall be in very durable tropical hardwood, greenheart or equal approved. The fantail structure at the rear of the mill shall be in dry good quality straight grained oak or other equally durable timber as approved.
After cutting all the joints and boring any holes, the cut faces of the timber shall be thoroughly treated with an organic solvent wood preserver before painting, and assembled with paint in the joints.
Refurbishment of sheers – front end.
After removal of the old weather beam the top surfaces of the two front sheers are to be cut down until firm solid timber is reached. The extent of the cut out to be determined on site. The cut out is to be faced up adequately to accept adhesive. A block of good quality oak or equal approved durable timber is then to be inserted and bedded on epoxy resin adhesive. The whole is then to be trimmed to the original timber section.
The ends of the sheers are then to be overlain with sheer planks in tropical hardwood 2.0 m long x 120 mm thick x 300 wide, bedded to the top of the shears in bitumen mastic and bolted to the sheers inside the cap. Following the installation of the sheer planks, the top and sides of the projecting timbers are to be sheathed with 1.5mm copper sheet bedded in mastic. The copper sheathing to extend to the inside of the cap. The cap roof is to be cut out only as far as necessary to accommodate the sheer planks and sheathing, and is to be made good and weathertight on completion.
Refurbishment of cap circle
A 1.5 m section of the cap circle beneath the central mullion is to be cut out and replaced in oak, with scarfed joints to maintain the continuity. Following this an oak spreader beam (with similar radius to the cap circle) is to be fixed to support the new mullion, in its raised position. The cap circle and spreader beam are to be fitted with care as they form the main load support to the centre of the weather beam and the windshaft main bearing.
Replacement of mullion.
The central mullion is to be renewed in greenheart of the same section as the existing timber. The top surface should be raised to be level with the new sheer planks. At its inner end it shall be jointed into the headstock using a bare faced tenon with the mullion lapped over the top and secured with a bolt. At the cap circle, the mullion will sit on the new spreader beam fixed above the renewed section of oak cap circle.
Replacement of weather beam and pillow block
The new weather beam shall be of tropical hardwood of 300 x 300 mm section and extending 50 mm past the outer faces of the shears. Each end shall be banded with a square hoop in galvanised steel section 40 x 8 mm, tightly fitted to prevent shakes developing. The weatherbeam shall fit above the sheerplanks and copper sheathing. Fixings to the sheers and central mullion shall each be by a single stainless steel through bolt 30mm dia, fitted with large square washer plates each end carefully gasketted with rot proof compressible material to ensure a waterproof seal to the hole through the timber.
The pillow block in tropical hardwood should be sized and bevelled to provide the correct level and slope for the main windshaft bearing.
Refurbishment of sheers – rear end.
After removal of the fantail structure the rear sheers are to be examined. Soft and decayed timber on the top surface is to be cut out down to firm solid wood and replaced with hardwood bedded on epoxy resin glue. The end joints of the timber are to be scarfed in at an angle 1in5. The whole is then to be trimmed to the original timber section and the top and sides sheathed in copper bedded in mastic
Reconstruction of fantail frame
The fantail structure is to be completely renewed using the original structure as a pattern. The timber used shall be dry good quality straight grained oak. Any deviations suggested by the tenderer to improve the life of the structure, for instance the detailing of joints to avoid water retention, shall be first discussed and approved by the employer.
The fantail platform and supporting joists between the sheers shall also be renewed in oak.
Fantail fan
A set of eight new fanblades are required to replicate the existing 3.5 metre diameter fan using 100 x 100mm oak arms and 25mm western red cedar boarding. The fanboards to be carried in slots in the arms, assembled with wet paint in the joints, and secured with bolts. The existing forged spacer bars at the tips of the fanboards to be cleaned, repainted in black and re-used with new fixing bolts. Fixed with new bolts in hub on existing shaft. The fanshaft and hub, drive shaft and gearing shall be cleaned and repainted in black.
Fixings
All screws, bolts and other fastenings passing through timber shall be stainless steel (BSS grade316). External fittings, such as timber bands and shackles shall be either stainless steel or heavy hot dipped galvanised mild steel.
Fixings for copper sheathing shall be in copper or as recommended by the Copper Development Association.
Paint
All paint shall be exterior grade stand oil paint as manufactured by either Kreidezeit as supplied by Mike Wye & Associates or Beeck as supplied by Ty – Mawr Lime Ltd. Finished shade of off white to be agreed with employer.
All paint shall be applied in accordance with the manufacturers recommendations for the particular type of timber used, and will include attention to surface preparation, priming, undercoating and finishing coats.
Wherever practical new hardwood and/or resinous timbers will be finished and then allowed to weather for a time and then thoroughly dried before final surface preparation by sanding and painting. Preliminary tests may be required to confirm details of application of paint system.
Prepared by JB, approved Operations Group
NOTE When the order was placed with Traditional Millwrights oak was substituted instead of Greenhart and lead used where copper is mentioned. Kreidezeit was used throughout. AFG
Appendix 2
Initial Estimate of Paint Requirements for sails (prepared by John Boucher)
item | no off | length | perimeter | l.p | total area | 15/litre | 15/litre | 15/litre | ||
Shutters | 126 | 1.8 | 0.66 | 1.2 | 149.7 | 0 | 0 | 9.98 | ||
Whips | 6 | 9.1 | 1 | 9.1 | 54.6 | 3.64 | 3.64 | 3.64 | ||
Sail bars + braces | 96 | 2.4 | 0.26 | 0.6 | 59.9 | 3.99 | 3.99 | 3.99 | ||
uplongs, Thimbles and rules | 30 | 7 | 0.2 | 1.4 | 42 | 2.80 | 2.80 | 2.80 | ||
________ | ||||||||||
306.2 | 10.4 | 10.4 | 20.4 | |||||||
4 cans | 4 cans | 8cans | ||||||||
Kreidezeit list price per 2.5l | £58.40 | £234 | £234 | £468 |
Total cost (sails only) estimated £948 plus Vat
Appendix 3
Actual purchase of paint, including used for cap, taken from HWS Accounts
Date | Type of Paint | Vol (L) | Price | VAT | Sub Tot |
02/12/2015 | Kreidezeit Base Oil | 10 | 101.52 | 20.304 | 121.824 |
02/12/2015 | Kreidezeit Stand Oil H/Rich | 5 | 105.12 | 21.024 | 126.144 |
02/12/2015 | Kreidezeit Stand Oil Full Rich | 5 | 105.12 | 21.024 | 126.144 |
02/12/2015 | Balsamic Turpentine | 1 | 9.36 | 1.872 | 11.232 |
02/12/2015 | Delivery | 21.95 | 4.39 | 26.34 | |
04/01/2016 | Kreidezeit Base Oil | 2.5 | 25.38 | 5.076 | 30.456 |
04/01/2016 | Kreidezeit Stand Oil H/Rich | 15 | 315.36 | 63.072 | 378.432 |
04/01/2016 | Kreidezeit Stand Oil Full Rich | 10 | 210.24 | 42.048 | 252.288 |
04/01/2016 | Delivery | 30.13 | 6.026 | 36.156 | |
21/01/2016 | Kreidezeit Stand Oil H/Rich | 5 | 116.8 | 23.36 | 140.16 |
21/01/2016 | Kreidezeit Stand Oil Full Rich | 7.5 | 175.2 | 35.04 | 210.24 |
21/01/2016 | Delivery | 17.68 | 3.536 | 21.216 | |
09/02/2016 | Kreidezeit Stand Oil H/Rich | 10 | 233.6 | 46.72 | 280.32 |
09/02/2016 | Kreidezeit Stand Oil Full Rich | 5 | 116.8 | 23.36 | 140.16 |
09/02/2016 | Delivery | 23.32 | 4.664 | 27.984 | |
Total incl Vat | 75 Litre | £1929.00 |
Appendix 4 – Paint data.
The following data is abstracted from current trade literature
Kreidezeit Stand Oil paint is a resin-free paint for interior and exterior wood and metal i.e. windows, doors, panelling, decorative features. It does not blister crack or flake, but stays elastic and wears down little by little. That is why it can be renewed even years after application with a minimum of effort by simply cleaning and applying another coat.
Stand Oil is a form of linseed oil created by heating it to 570 degrees Fahrenheit in an oxygen-free atmosphere. This causes partial polymerisation increasing its viscosity, which is about the same as honey.
The technique of application used on the sails was to obtain a layer structure of application and is essentially a three coat system, ‘lean’ to ‘rich’ –
- Base Oil – penetrates deeply into the wood
- Half-rich intermediate coat – extremely highOpacity
- Full-rich finishing coat – long lasting weather Protection